top of page


TOASTER REDESIGN
The goal of this project was to break down a generic toaster to understand its design and manufacturing considerations in order to improve the design to optimize user experience and manufacturing. We designed a toaster that redefines the way users interact with toasters while reducing assembly time and cost by 44% and 37% respectively.
My Role
MY ROLE
USER RESEARCH
I studied the user needs and requirements which helped us in understanding what the customers really want and the importance levels attached to various requirements.
​
COMPETITORS ANALYSIS
Going through a myriad number of customer reviews of our generic toaster and the market leaders in sales and ratings allowed us to get a deeper understanding of what our product lacked and how we could make it better. This research helped us identify the functional requirements of the product which proved instrumental in our redesign.
PRODUCT DESIGN
I played a fundamental role in product design efforts by building a architecture for the product. By building a platform and providing the team with design guidelines, we were able to make the design process smoother and time efficient.
​
CONCEPT DEVELOPMENT
I led the concept development by creating a CAD prototype of our redesigned product. This allowed the team to visualize the concept better enabling more constructive changes and improvements to be made.
Problem Statement
THE CHALLENGE
IMPROVE TOASTER DESIGN
This six week academic project saw us analyze a generic toaster from a design for manufacturing, assembly and sustainability standpoint. The objective was to learn the influence of materials, manufacturing processes, production costing and product life cycle in the design and development of a product.
​
Through our analysis of the generic toaster and the application of these concepts, we were challenged to redesign the humble toaster.
The guiding principles were:
-
The toaster must enhance user experience
-
The toaster must be faster, easier and cheaper to manufacture and assemble
-
The toaster must employ the use of materials and manufacturing processes with minimal adverse impact on the environment

Solution Approach
THE APPROACH
STAGE GATE
Given that this was an academically motivated project, we took a linear approach to this project. There were four major stages of this project.
Stage 1 (Toaster Functional Decomposition): Disassembling and reassembling the generic toaster to record and analyze the various components, their orientation and assembly sequence.
Stage 2 (Toaster Quality Function Deployment): Involved the identification of customer needs, product requirements and competitor analysis.
Stage 3 (Material & Manufacturing Process Selection): Three components were analyzed in detail for the redesigned toaster. Materials and manufacturing processes were researched and selected.
Stage 4 (Concept Development): A final concept is developed to showcase the redesigned features.

STAGE TWO: QUALITY FUNCTION DEPLOYMENT
​
​
Stage One
STAGE ONE: TOASTER FUNCTION DECOMPOSITION
​
We began by disassembling the generic toaster that was provided to us. Each step of the disassembly was recorded and each component identified and labelled.
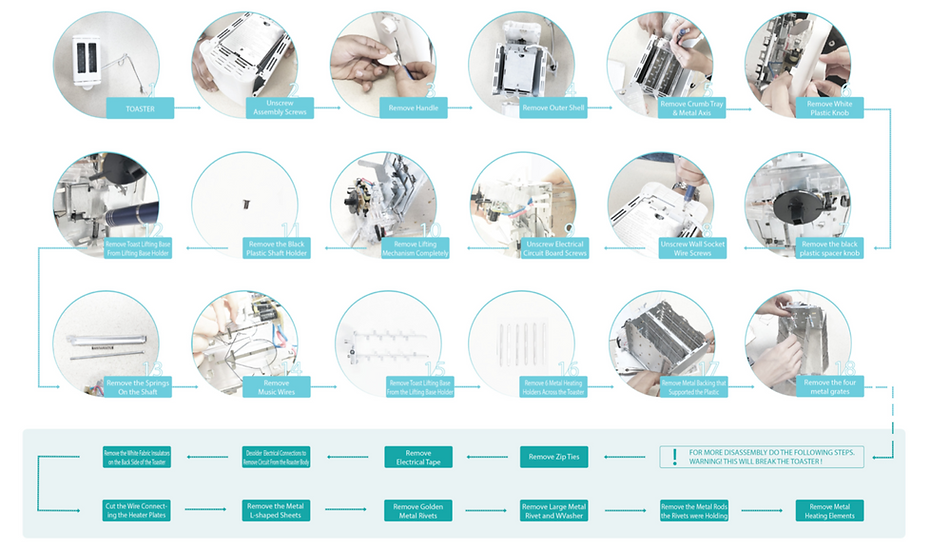
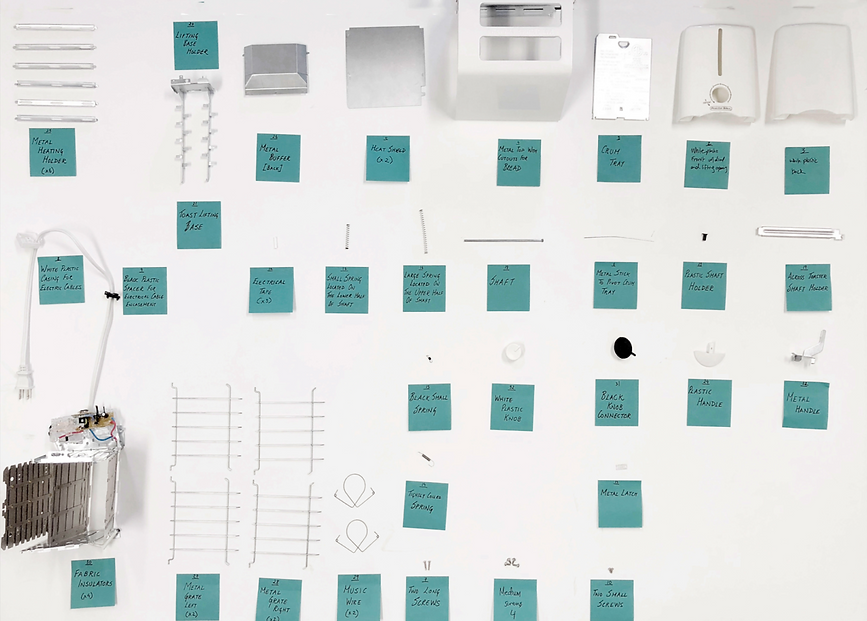
For each component that was disassembled, the material and manufacturing process used for that component were identified as accurately as possible. Next, the component was analyzed for its importance to the toaster assembly, i.e. could the toaster be made without it. For this, three key questions were asked:
-
Does the part move relative to other parts during normal functioning of the toaster?
-
Must the part be made from a different material?
-
Does the part need to be separate for manufacture or repair?
If the answer to all three questions was NO, the component was not essential. These components would be called Candidates for Elimination (CFE).
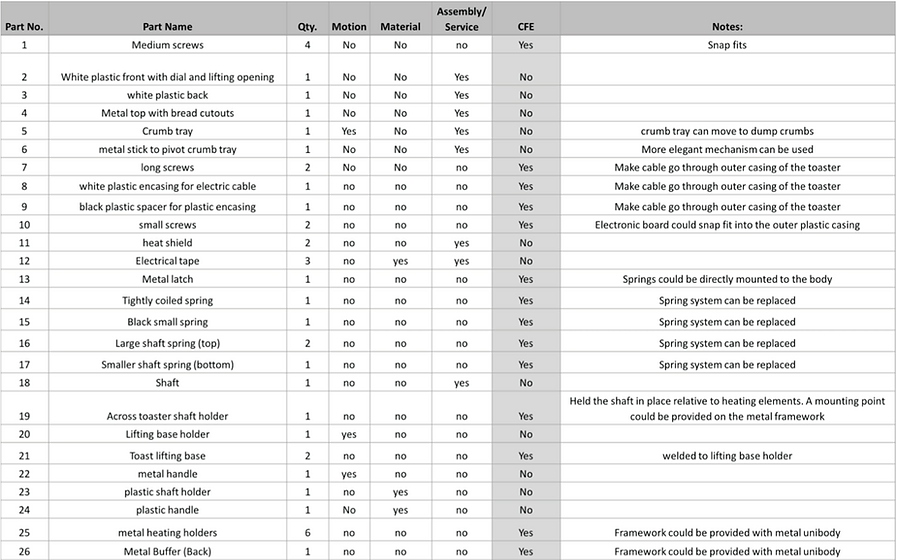
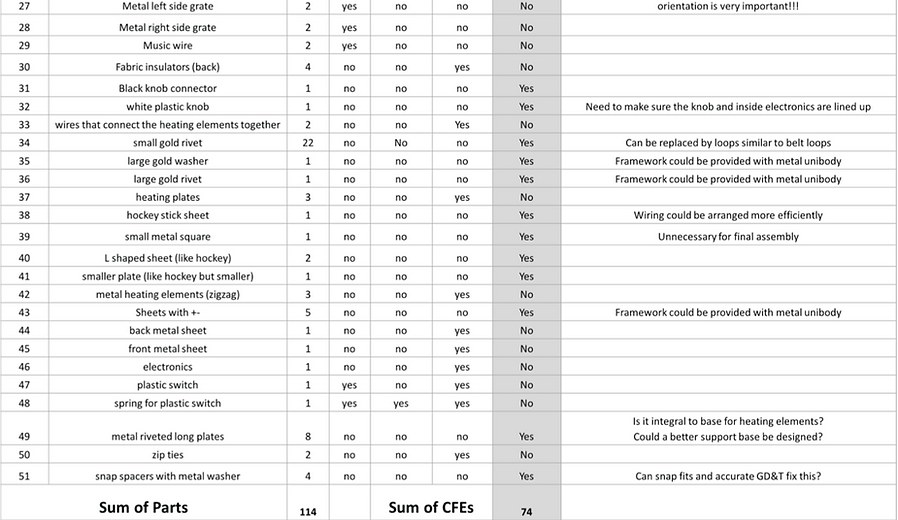
This analysis shows a 35% part count efficiency indicating that 65% of the parts are not absolutely necessary to the toaster and can hence be eliminated if the toaster was to be redesigned efficiently.
While some of the components may be truly unnecessary, others could be merged together. For example, metal heating elements and the rear buffer could be combined in a metal unibody. The same is true for the plastic elements like the toaster knob and the electrical components. Additionally, the number of screws could be significantly reduced or eliminated by the use of snap fits.
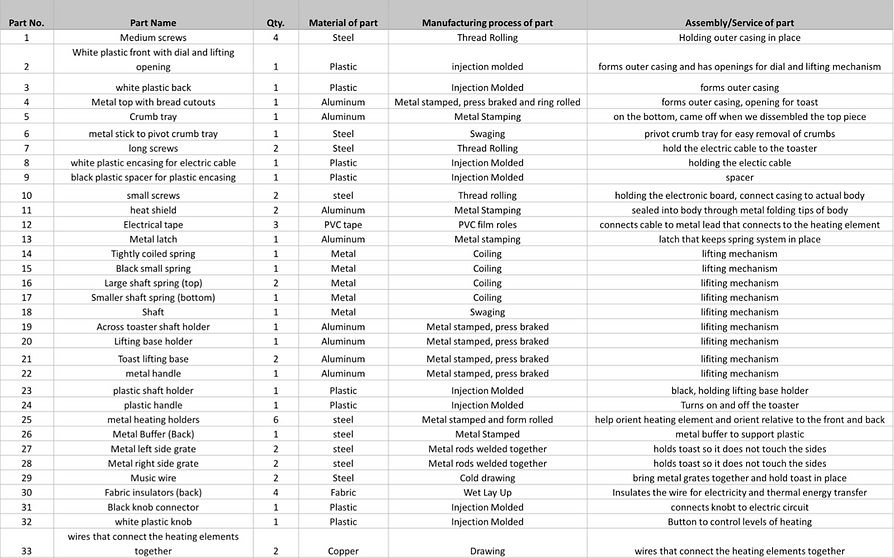
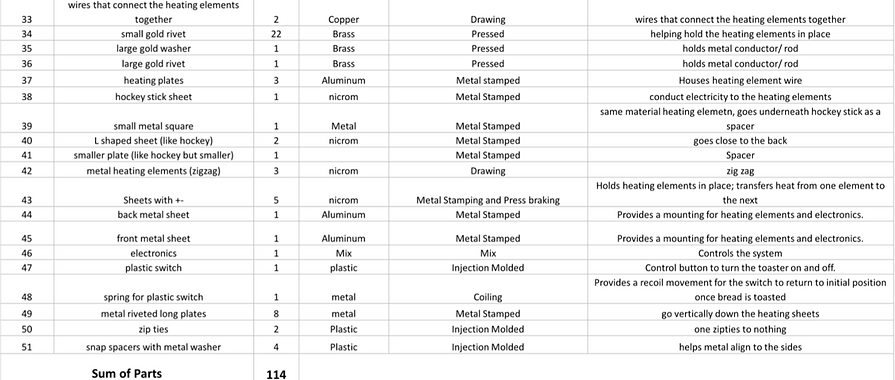
Stage Two
CUSTOMER REQUIREMENTS
Through an extensive exploration of user reviews on Amazon and Best Buy we identified a set of features that customers deemed necessary be in their toasters. Sifting through over 200 user reviews, we identified the following as the core customer requirements. These would later be used to build a House of Quality or a Quality Function Deployment.
We analyzed the functioning of a toaster to identify the crucial functions that are being performed. Forming a list of functional requirements, we built a flowchart to better help us understand the various steps involved in the operation of a toaster. This understanding would form the foundation of our redesign.

FUNCTIONAL REQUIREMENTS

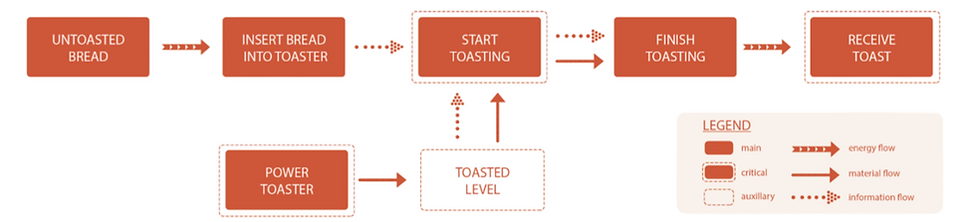
Competitive Analysis
COMPETITOR ANALYSIS
In order to get a grasp of how this generic toaster (Proctor Silex) performs relative to its competition, we selected the top selling and the top rated toasters on Amazon to conduct a competitive analysis. This competitive analysis enabled us to understand competitor’s strengths and weaknesses in regards to the customer needs and requirements.
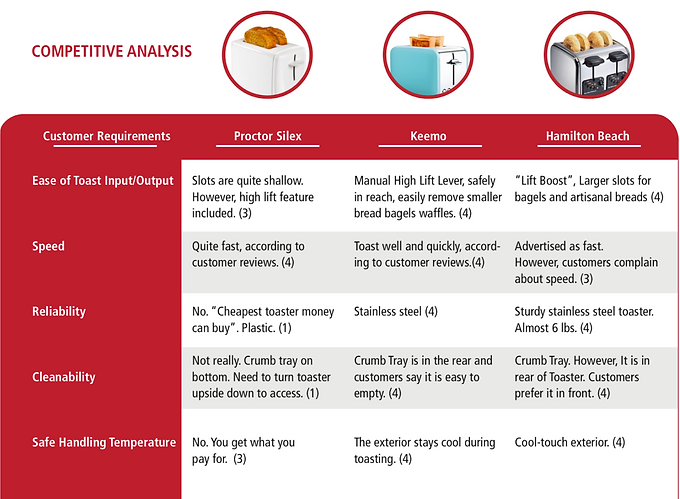

House of Quality
HOUSE OF QUALITY
Following a competitor analysis, we perform a Quality Function Deployment study. This is accomplished through the construction of a House of Quality.
​
This is a process that translates the customer’s voice into metrics helping devise a plan to prioritize steps of execution based on what is important to the customer. This process also helps establish a relationship between functional requirements enabling an easier prioritization based on pragmatism.
​
Finally, the house of quality also helps establish the competitor performance based on the metrics identified through customer requirements.

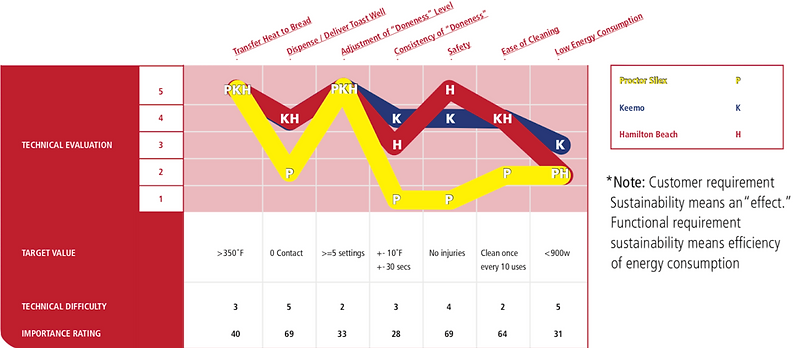
QFD RESULTS
​
-
With a rating of 69, one of the top requirements was that we redesign the toast dispensing mechanism.
-
Jointly with a rating of 69, was safety. This indicated that it would be prudent to use materials that are good insulators of heat. This could allowed us to explore sustainable materials such as wood. This indicated a need to redesign the outer casing of the toaster i.e. the touchpoint of the user.
-
With a rating of 64, cleanability was one of the top requirements as well. The generic toaster needed to be lifted up of the counter top to clean making it inconvenient and inefficient. This pointed at a need to redesign the crumb tray.
STAGE THREE: MATERIAL & MANUFACTURING PROCESS SELECTION
Stage Three
For each major component that was to be redesigned, a detailed analysis was conducted in order to enable the optimum selection of the material and its corresponding manufacturing process. The analysis was conducted through the following steps:
-
The primary attributes for that part were hypothesized
-
A primary and secondary material was selected.
-
For each material option, its top three performance attributes were listed along with target values
-
The pros and cons to each material were identified
-
A primary and secondary manufacturing process was listed along with a brief reasoning
DISPENSING MECHANISM

Credit: Brian Xiao
Our new design proposes a spring loaded drawer that enable the user to open the toaster in two halves, put the bread in and the have the two halves close, holding the bread tight. With this design, when the toast is done, the user simply opens the toaster again and the toast falls onto the plate below. The spring loaded drawer uses four telescoping rods to connect the two sides of the toaster to each other.
DISPENSING MECHANISM - MATERIAL
PRIMARY OPTION: Stainless Steel 304
TOP ATTRIBUTES​
-
Safe for food
-
Easy to manufacture
-
Material Strength
TARGET VALUES​
-
Handles upto 500° C without melting
-
No unwanted reaction to chemicals in food
-
Ultimate Tensile Strength = 310 MPa
PROS​
-
High corrosion resistance
-
Higher strength and hardness at high temperatures
-
Ductile
CONS​
-
Shows smudges and fingerprints
-
Unstable prices
SECONDARY OPTION: Aluminum 6061 - T6
TOP ATTRIBUTES​
-
Non-stick surface
-
Safe for food
-
Durable
TARGET VALUES​
-
Handles upto 500° C without melting
-
No unwanted reaction to chemicals in food
-
Ultimate Tensile Strength = 310 MPa
PROS​
-
100% recyclable with no downgrading of quality
-
Non-toxic
-
Easily available
CONS​
-
Higher assembly costs
-
Energy intensive extraction process from raw materials
DISPENSING MECHANISM - MANUFACTRING
Primary Option: Metal Stamping
Metal stamping is a cheap and widely used manufacturing process. The rapid cycle time makes this process very efficient for high volume production. High tooling costs are balanced by high accuracy.
​
Secondary Option: Deep Drawing
Deep drawing has a rapid cycle time and is good for medium to high volume processes. Since we have a relatively simple part, this process can be utilized.
CRUMB TRAY

Credit: Brian Xiao
The crumb tray is a metal collection sheet that collects crumbs and allows user to dispose of them after use. Our redesigned crumb tray functions as a crumb drawer that is accessible from the front of the toaster. This allows users to remove it easily to dispose of the crumbs.
CRUMB TRAY - MATERIAL
PRIMARY OPTION: ABS Plastic Frame with Aluminum 6061 - T6 Tray
TOP ATTRIBUTES​
-
Poor conductor of heat
-
Non-stick
-
Durable
TARGET VALUES​
-
Heat Transfer Coefficient = 204 W/mK
-
Ultimate Tensile Strength = 310 MPa
PROS​
-
100% recyclable with no downgrading of quality
-
Non-toxic
-
Easily available
CONS​
-
Higher assembly costs
-
Energy intensive extraction process from raw materials
SECONDARY OPTION: Magnesium Alloy
TOP ATTRIBUTES​
-
Poor conductor of heat
-
Strength
-
Lightweight
TARGET VALUES​
-
Heat transfer coefficient = 159 W/mK
-
Density = 1.738 g/㎤
-
Ultimate Tensile Strength = 228 MPa
PROS​
-
Better strength to weight ratio
-
Lightweight
CONS​
-
Expensive extraction process from raw material
-
Explosive in powder form
-
Prone to corrosion
CRUMB TRAY - MANUFACTRING
Primary Option: Metal Stamping & Injection Molding
Metal stamping is a cheap and widely used manufacturing process. The rapid cycle time makes this process very efficient for high volume production. High tooling costs are balanced by high accuracy.
​
Injection molding is a high volume, rapid manufacturing process with high quality and accuracy of plastic parts.
​
Secondary Option: Metal Stamping & Anodizing
The anodizing process will be used since it is able to protect magnesium from corrosion whilst affording it a smooth to touch finish. This process builds a natural oxide layer which is self-healing and light. The cost of anodizing metals is not very expensive however it is time consuming.
CLEAR CASING
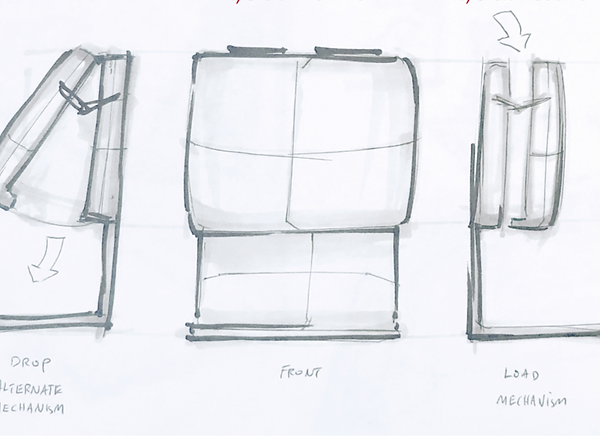
Credit: Brian Xiao
The clear body will allow the toast to be viewed by the user, letting them visually see how well done the toast is. This is an indicator to show people more clearly, what is happening to their toast allowing the user to know when the toast is ready.
CLEAR CASING - MATERIAL
PRIMARY OPTION: Borosilicate Glass/Pyrex
TOP ATTRIBUTES​
-
Safe for food
-
Financially feasible
-
Resistant to high temperature
TARGET VALUES​
-
Chemically inert to food acids
-
Low Cost: $24 per sheet (14 in. x 17in.)
-
Operating temperature range: 230° C to 500° C
PROS​
-
High softening point (800° C)
-
Stronger than soda-lime glass if extruded
-
Resistant to food acids
CONS​
-
Difficult to mold and fabricate
-
Chances of breaking
SECONDARY OPTION: High Performance Glass
TOP ATTRIBUTES​
-
Resistant to high temperatures
-
Non-reactive with food
-
Durable
TARGET VALUES​
-
Operating temperature range 700° C - 800° C
-
No unwanted reaction to chemicals in food
-
Ultimate Tensile Strength = 212 MPa
PROS​
-
Harder and more durable
-
Resistant to rapid temperature change
-
Chemically inert
CONS​
-
High costs
CLEAR CASING - MANUFACTRING
Primary Option: Water Jet Cutting
Abrasive waterjet cutting is an accurate cold cut process without leaving a heat affected zone. A wide range of material thickness can be cut since waterjet cutting is able to cut material from 0.002” to 12” . It can achieve high accuracy of up to +/- 0.001.
​
Secondary Option: Glass Blowing
Glass blowing has a fast cycle time when mechanized and high quality can be achieved. Although the tooling costs are high, the price per unit is much lower for mechanized processes. This is a food safe material process and the final product is produced so that food is able to touch the surface.
Concept
STAGE FOUR: CONCEPT DEVELOPMENT
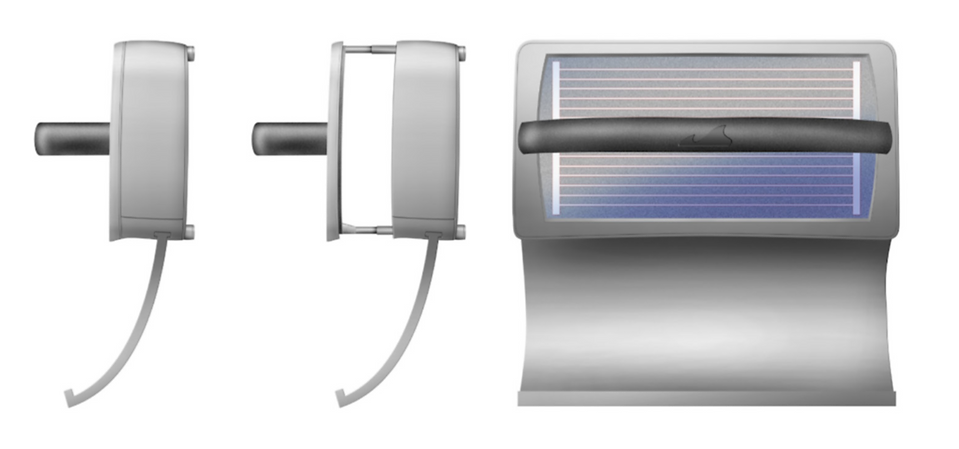
My Learning
WHAT DID I LEARN ?
In undertaking this project I was surprised to learn about the immense complexity a simple device that we use daily can have. It was an eye opening experience to learn about the inefficiencies of some of the mass produced products on the market.
In redesigning the toaster, I learnt to apply the various principles and methodologies that enable good decision making based on downstream considerations such as robustness, safety, cost and product development process. I am now able to understand how design choices are affected by material and manufacturing process selection.
I have learnt the ability of utilizing customer feedback to build metrics that can help in product evaluation and development. This is crucial in adding a level of tangibility to abstract and intangible information.
bottom of page